These are all customized products according to
customer's requirement. If needed, we can
provide custom sevice for you.
The oil leakage points of this type of seal are:
1) Leakage at the seal between the support seat and the bearing seat.
2) Leakage at the seal between the output shaft and the shaft hole of the end cover.
reason:
1) Quality problems of the oil seal: poor elasticity of the oil seal, defective lip, loose spring or falling off.
2) The lip of the oil seal is flanged or trimmed due to assembly; or the tightening torque of the connecting bolts of the oil seal seat is insufficient.
3) The processing quality of parts and components.
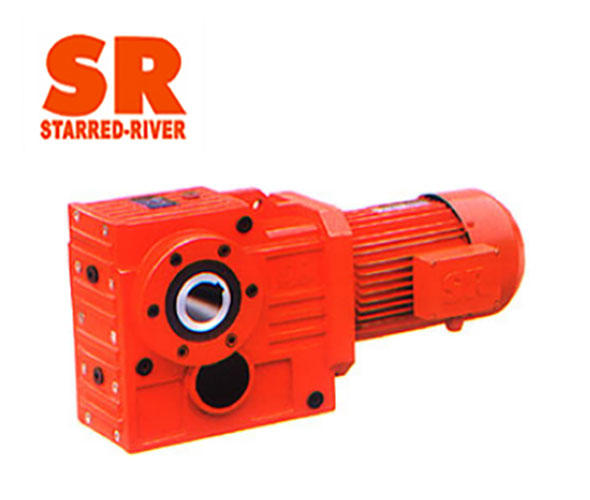
Treatment measures:
1.1 Select qualified oil seal products produced by regular manufacturers.
1.2 Use special oil-sealed assembly tooling and assembly methods in assembly.
a) When selecting tooling, pay attention to the contact position between the tooling and the oil seal. If the diameter of the contact is too small, the oil seal lip will be deformed.
b) It is also necessary to apply the force in the correct way. Use a suitable size pad to apply pressure evenly in the diagonal direction. Remember not to hit the oil seal directly to avoid deformation of the oil seal.
c) During the assembly process, attention should be paid to ensure the level of the oil seal, so that the oil seal is evenly pressurized in the cavity, so as to ensure the effectiveness of the seal. If the oil seal is forcibly pressed into the cavity, the fitting part of the sealing lip of the oil seal will be squeezed and stuck, resulting in oil leakage.
1.3 Use a special pneumatic wrench to tighten the bolts, and use a torque wrench for testing.
1.4 Design of the sealing part of the parts:
a) The principle of the interference between the lip and the shaft: usually the shaft diameter is less than 20mm, the lip interference is 1mm; the shaft diameter is greater than 20mm, the interference is 2mm. The interference between the outer diameter of the oil seal and the shell should be 0.15mm to 0.35mm;
b) The contact width between the lip and the shaft: when the pressure difference is not large, the contact width of the lip is 0.2mm to 1mm; if the medium pressure difference is large, the contact width should be increased.
c) The roughness of the shaft is required to be 0.8 μm to 3.2 μm. If the surface is too smooth, the oil is easily squeezed out from the sealing contact surface, and the oil film becomes thin or disappears, causing the lip to heat up or burn out; otherwise, the lip wears too fast, causing leakage.
1.5 The design optimization of the structure can adopt the sealing form of floating oil seal.
Floating oil seals are often used in planetary reducers to dynamically seal the end face of the component. The floating oil seal is a mechanical seal, generally composed of a floating ring of ferrous alloy material and a matching nitrile rubber O-ring. The floating ring is used in pairs, one rotates and the other is relatively static.
The sealing principle of the floating oil seal is that the two floating rings are deformed by the axial compression of the O-ring, which produces a pressing force on the sealing end face of the floating ring. With the uniform wear of the sealing end face, the elastic energy stored by the O-ring is gradually released, thereby playing an axial compensation role.